Food flooring—a critical element of the food business
Label stamping, CIP washes, blast chilling, splashes of hot grease—these factors hit the floor daily at meat processors, bakeries, and cheese plants. Ordinary concrete or tile cracks, absorbs proteins, and turns into an incubator for pathogens, while any crack will fail an HACCP audit. Food-grade floors are seamless polyurethane-cement or epoxy systems certified under EU 10/2011 and FDA; they withstand –13 °F (–25 °C) in a shock freezer and +250 °F (+120 °C) under a steam kettle without deformation. Their glass-like matrix absorbs neither blood nor acids, and the deep profile remains non-slip even after a thousand Taber abrasion cycles.
What advantages does the coating offer?
Before ordering, consider the key benefits of this flooring type. Laboratory reports and customer reviews confirm the following:
- Color is integral to the mix, so even a chip shows the same shade, not “cement gray.”
- A seamless monolith eliminates settling and weed growth, saving on herbicides and joint sand.
- F200 frost resistance guarantees no pitting after “thaw–freeze” cycles.
- A full 1,076 ft² (100 m²) job takes 3–4 days: prep, pour, texture, polyurethane topcoat.
- Maintenance is reduced to renewing the protective layer every 3–4 years, which takes just one workday.
In the very first season the facility gets a floor that keeps uniform color in sunlight, doesn’t spall under forklifts, and cuts sanitation-chemical costs by about 15 %. That’s a proven KPI, not a theoretical promise.

Contact us!
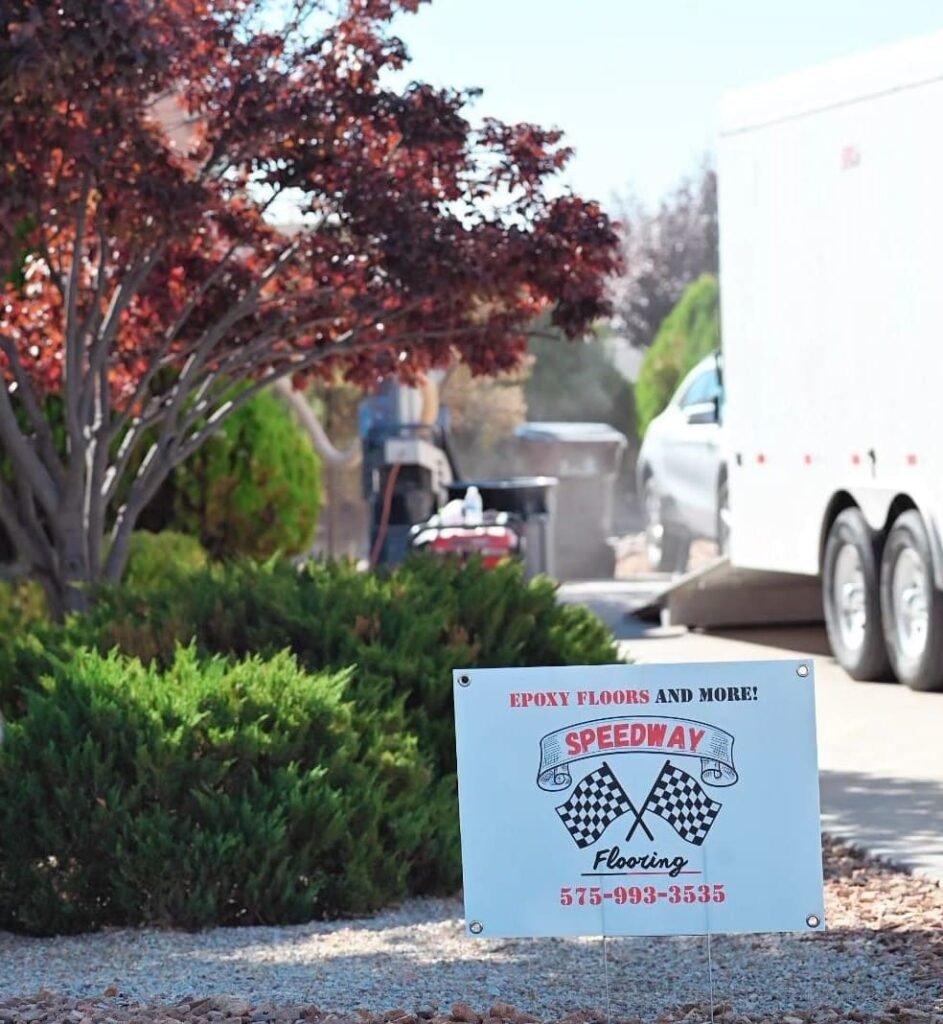
Food flooring installation process
We work turnkey: from a free risk audit to issuing validation documents for regulators. Every site receives its own formula—polyurethane-cement for “wet” zones, antistatic epoxy for packaging lines, or an MMA system that cures fast enough to reopen an area in 24 hours.
First, technicians mill the substrate, vacuum the dust with industrial turbines, and apply a hybrid primer. Next, they lay reinforcing mesh, add fiber, and pour a 3/8–1/2 in (10–12 mm) base layer. After leveling, the surface is broadcast with quartz of the chosen grade and sealed with a food-safe polyurethane topcoat. Within 12 hours the floor is ready for light foot traffic, and after 48 hours for full trolley service.
Applications and economic impact
The coating performs equally well in 3,200 ft² (300 m²) artisan cheese rooms and 215,000 ft² (20,000 m²) plants. The most telling cases—where the flooring pays for itself in under three years (sometimes sooner, considering reduced product loss from microbiological risks)—include:
- Dock ramps and –13 °F freezers where regular tile cracks.
- Decks near steam kettles and fry lines with floor temps up to +250 °F.
- Breweries, wineries, and coffee roasters where CO₂ and organic acids destroy concrete.
- ISO 7 cleanrooms for cultures, supplements, or baby food.
- Fish and meat defrosters where salty water spray corrodes joints.
In each scenario the monolithic slab handles passenger-car point loads, resists acids and alkalis, and cleans with high-pressure washers without abrasives. A wide palette of colors and quartz blends lets you zone production areas by floor color, simplifying visual cross-contamination control.
After commissioning, we leave a care checklist and an official warranty on integrity and color.
Order a free audit today: a Speedway engineer will arrive with samples, a fixed estimate, and a ready timeline. This flooring combines laboratory sterility, the strength of an industrial slab, and modern polymer aesthetics. Your plant, warehouse, or restaurant will get a surface that maintains flawless appearance and safety for decades.
Professional Concrete Crack Repair in Las Cruces, NM – Speedway Coatings
Call (575) 993-3535 now to schedule your free assessment and get a fixed quote. Let’s get your concrete back in shape—reliably, efficiently, and built to last.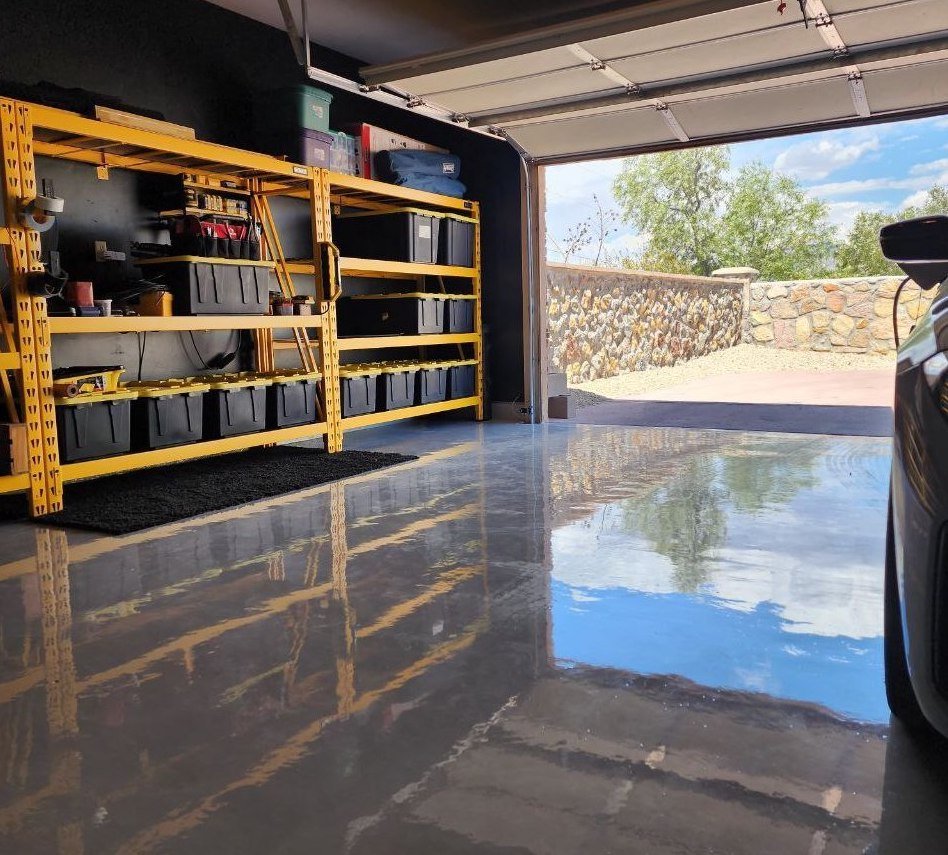
ABOUT US
Professional Flooring Service in Las Cruces, NM
You can’t go wrong by hiring us at Speedway Flooring for your next floor project. We take pride in our excellent craftmanship and our dedication to customer service. You’ll appreciate that we are:- Certified Epoxy Floor Coating Installers
- Dust-free equipment
- Expert, guaranteed workmanship
- We offer options for pricing on every project
- Provide free estimates
Our Services
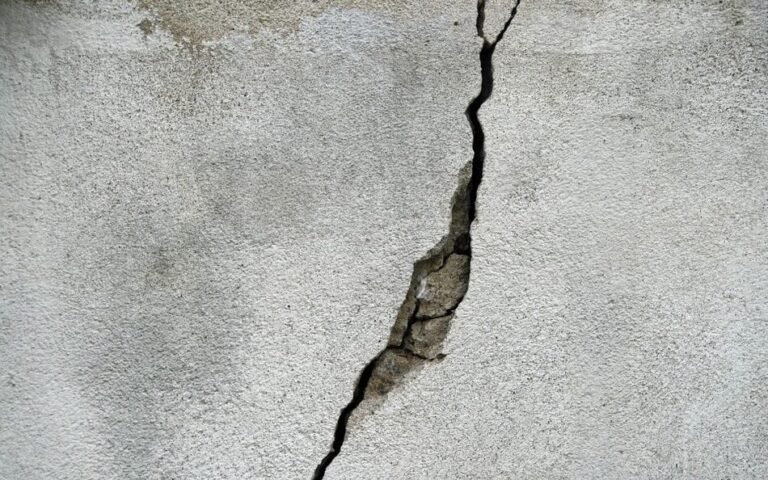
Concrete Repair
Cracks in your concrete may not worry you now, but they can lead to bigger issues down the road. If you’re dealing with concrete damage, turn to the pros at Speedway Flooring.
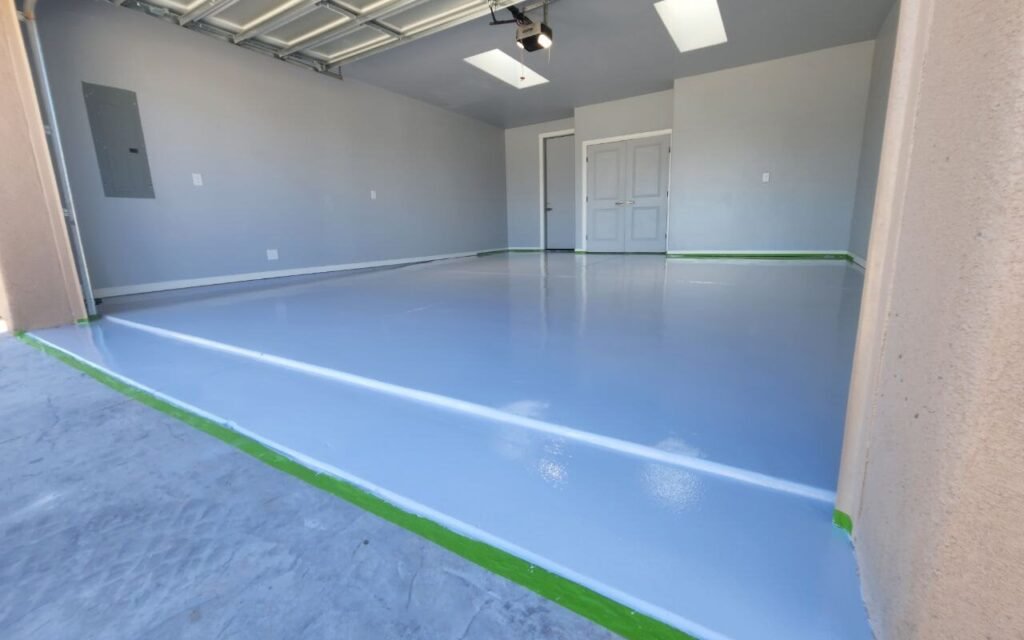
Epoxy Coatings
It is highly durable, customizable, sustainable, and decorative for any surface. It is commonly used for commercial and industrial flooring as well as residential and is normally applied over concrete floors.
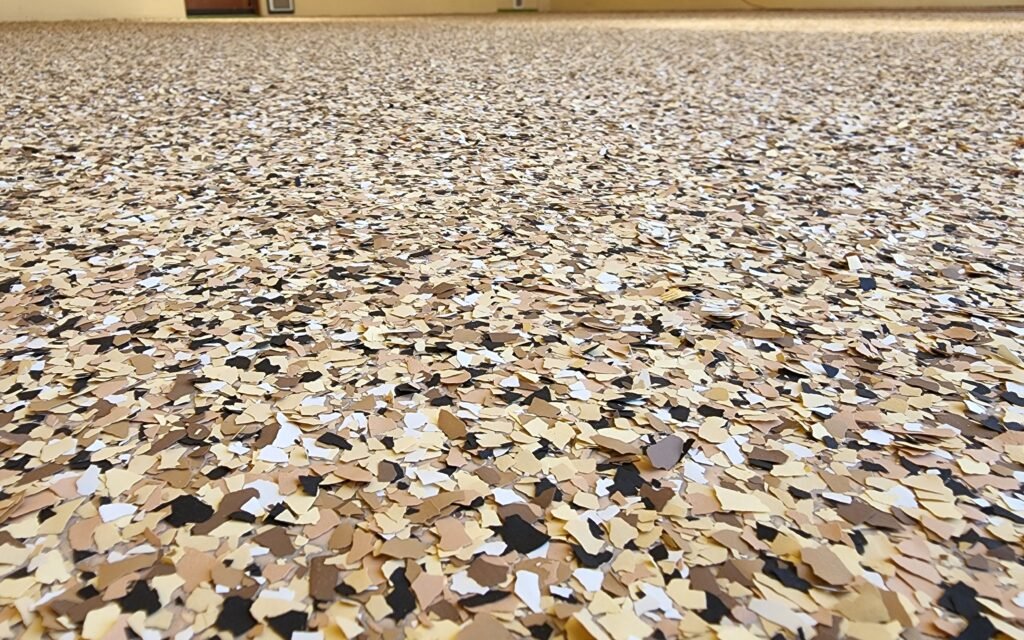
Concrete Repair
Cracks in your concrete may not worry you now, but they can lead to bigger issues down the road. If you’re dealing with concrete damage, turn to the pros at Speedway Flooring.
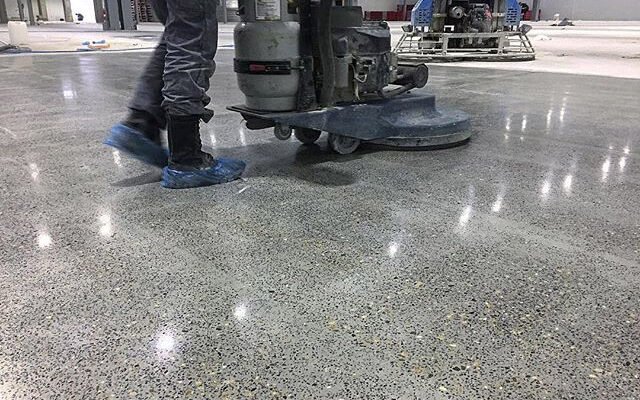
Concrete Polishing
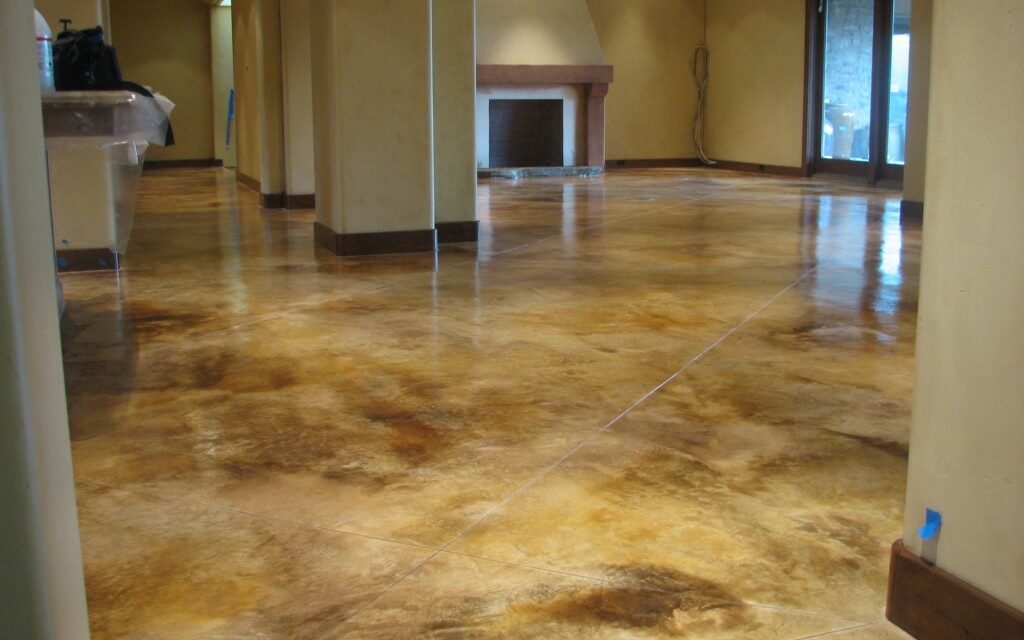
Stained Concrete
Stains can be used to achieve a range of different effects from subtle mottled patterns to vibrant, deep colors.
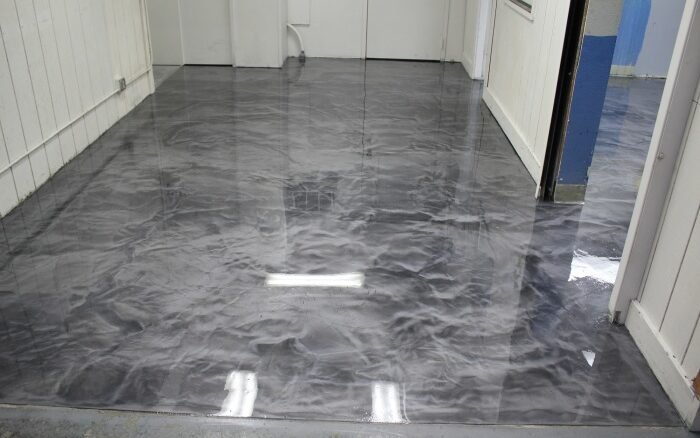
Metallic Epoxy Floors
The type of flooring system that combines the durability and strength of epoxy with unique metallic pigments to create a visually stunning surface.

All our work is DUST-FREE!
The process of preparing and grinding concrete can be very dusty. Crystalline silica is found in materials such as concrete, masonry and rock. When these materials are made into a fine dust, it is not only difficult to clean, but breathing in these fine particles can cause lung damage. Our high quality grinders and vacuum systems will collect dust during the grinding process, so you don’t need to worry about having dust on the walls or windows after we leave!
Visit our Instagram page to see videos of this great machine at work!
Working Process

Quick Request
You send us a request through e-mail or call our specialist to request a quote.

Inspect & Analise
We come to your house or business to measure the job site. We analyze the the condition of the concrete and amount of foot traffic to offer you the best floor solution.
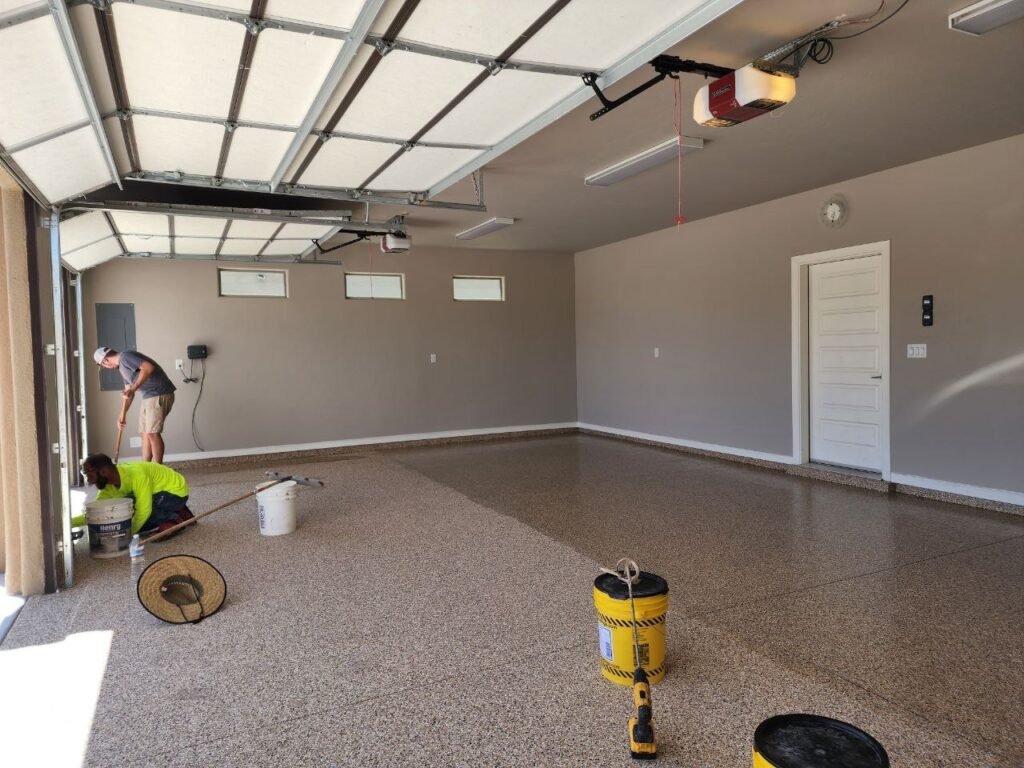
Preparation of The Concrete
After you approved our quote and picked the color, we begin our work process. We remove all the previous coatings, if you had on the floor, grind the concrete, and fix all the existing cracks.
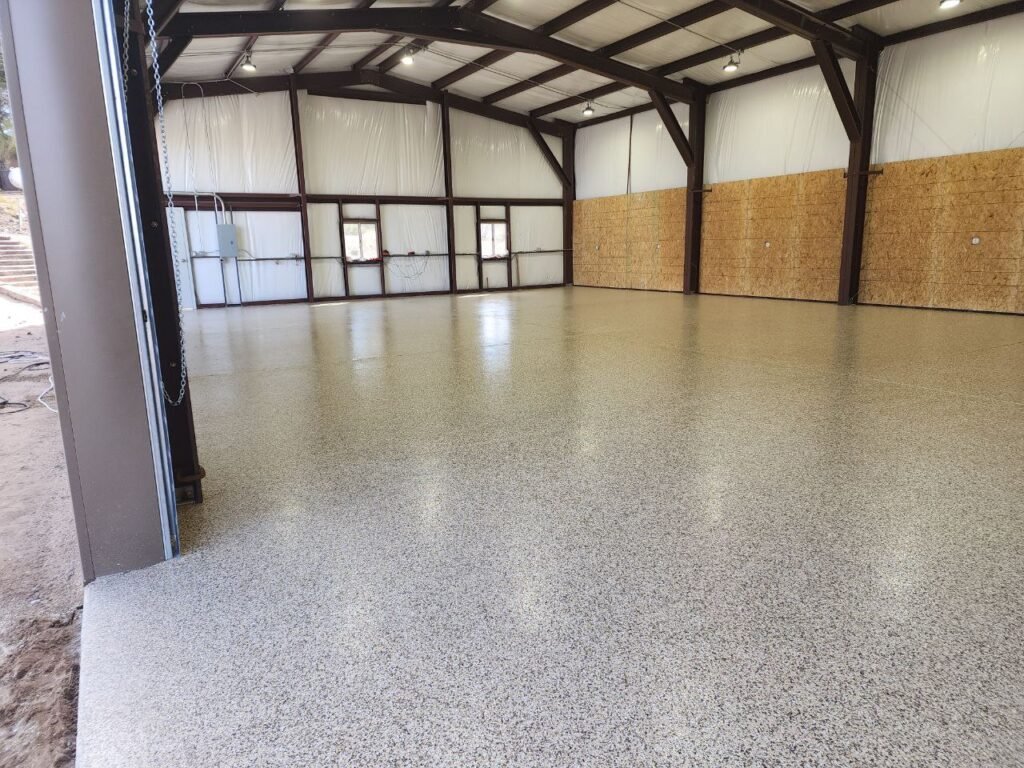
Finish
Then, depending on what you chose, we coat, polish or stain the concrete and finish with the sealer.
Call us today!
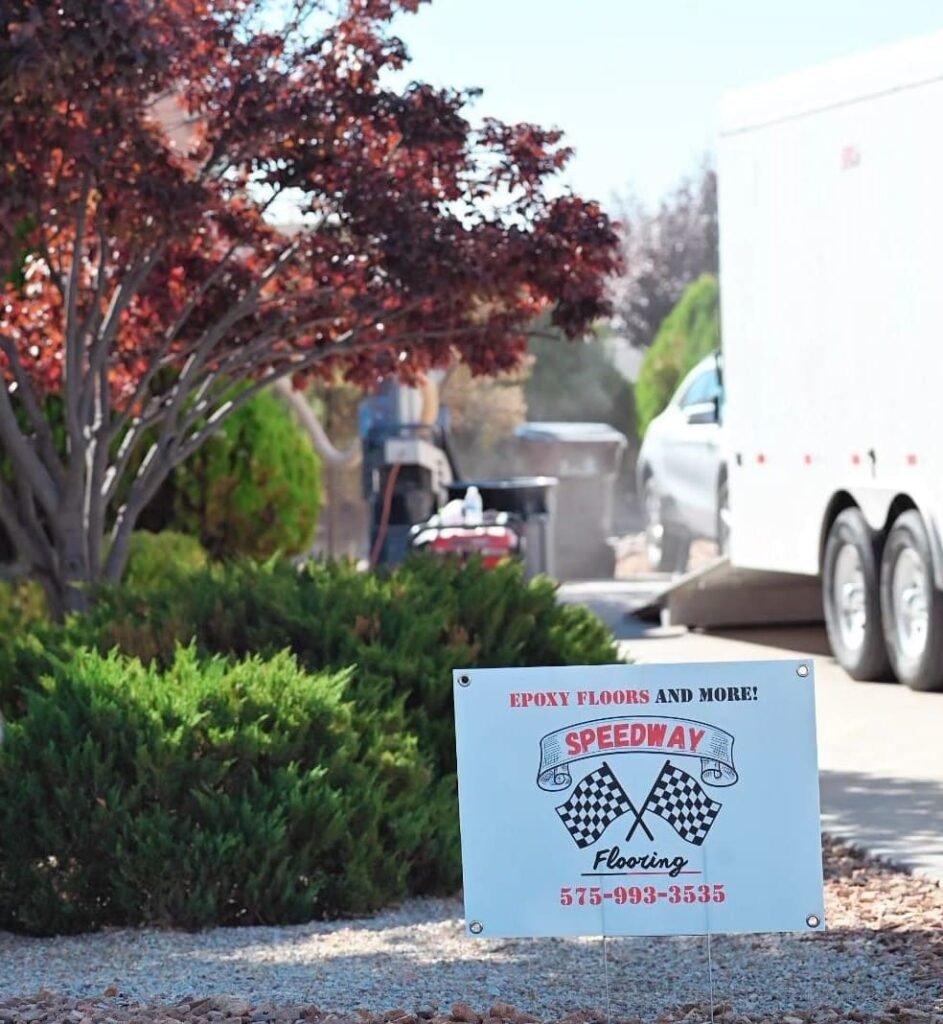
FAQ
What substrate prep is needed for Food Flooring, and how are control joints handled?
Specialists grind the concrete to “clean aggregate”, vacuum it, and prime with a deep-penetrating hybrid primer. Existing cracks are routed and filled with an epoxy repair compound. In new slabs, we cut joints only around the perimeter and near columns; inside the production zone, the coating remains monolithic, eliminating lines that collect dirt and moisture.
Will the floor withstand daily CIP washing with hot caustic foam and disinfectants?
The polyurethane-cement system tolerates pH 2–13 and temperatures up to +250 °F, so alkaline and acid washes neither leach color nor delaminate the surface. Simply renew the protective topcoat every 3–4 years—the procedure takes one day and requires no equipment removal.
How long will the shop be idle during installation?
A site up to 1,076 ft² (100 m²) is delivered in 3–4 days: day 1—mechanical prep and primer; day 2—base pour; day 3—topcoat and cure. After 12 hours you can walk on it, and after 48 hours the floor is ready for pallet jacks, forklifts, and thermal processes.